Managing a facility within the CPI demands that a manager keeps his/her balance in an environment that is now being buffeted by constant change: digitalization, sustainability, merciless competition from all four corners of the world, and rapid evolution of process technologies (process intensification, shrinking time to market constraints).
Operational Issues:
Managers know that operational issues come in three flavors:
1 – Major technical deficiencies that create process upsets,
2 – Creeping inefficiencies that drain away profitability, and
3 – Internal/external business/operational practices that lead to inefficient use of time and resources.
In some cases, these issues are local, within the plant itself; others, the issues start at the top.
1 – Technical Deficiencies seen in Process Upsets: Managers know all about process upsets. They are an unfortunate part of a chemical plant’s existence, no matter how well run or managed. Process upsets will occur, and they need to be respected and controlled. They are in the fabric of a plant’s operations in spite of all the advanced technology intended to keep operations smooth and stable.
An upset can be caused by any number of process-related issues that disrupt the smooth operations of a chemical process. An upset can be a minor issue such as a small temperature excursion which can lead to an off-spec product. It can also be a major deviation, such as an unexpected exothermic reaction, which can compromise both plant equipment and worker safety if not quickly identified and rectified. It can be the malfunction of a formerly reliable piece of equipment that causes a rapid plant shutdown. Whatever the cause, process upsets, at the minimum cost time and money. At the worst, they can create mass casualties, destruction of infrastructure, and permanent unfavorable publicity.
2 – Creeping Inefficiencies: Even worse for the long-term viability of a plant is the slow drip-drip-drip of a seemingly well-established process incrementally, almost imperceptibly, going south. An operation that has consistently generated profits suddenly becomes the red-headed child. Resources are thrown at the perceived problem, but resolution seems to move further and further away. Unlike upsets, which announcement themselves pretty unambiguously, underlying technical issues sneak up from behind; in fact, sometimes they are not even perceived to have happened….their only calling card is degenerating process effectiveness.
3 – Business Practices and Conventions that get in the way of smooth operations. It is a human characteristic to grow complacent with the way things are – to stop seeing the forest for the trees, and not to see budding issues. Business Transformation is a broad topic that allows personnel to see transactional issues with impartial eyes. For the chemical industry, transformation might have several different characteristics. It involves upgrading “the business of running a business”:
-
Adapting to new regulations,
-
Changing how workflows are established: inventory tracking, internal material flows, enhancing inter-personal communications between and within departments and reducing silos,
-
Adjusting to changing customer expectations,
-
Operating in a more sustainable way and enhancing the utilization of human resources.
But – even more important is that plant management understand the need to always look at their technical and business processes with new eyes. We all have the experience of the old adage “familiarity breed contempt”. When we drive to work or return home via a new route, we are very sensitive to all the subtle things we encounter on the way – curves, stop signs and lights, pedestrian crossings, etc.
As we gain familiarity, we lose that sense – we stop noting things along the way and we tend to become befogged. If we see something new or unexpected, we tend NOT to see them. That’s why when a new traffic light is added to a street, great pains are taken by the local DOT to really flag that change. Otherwise, drivers will roll right through the light without even realizing it’s there. We see tragedies weekly when babies are left in hot cars during the summer because a parent, stuck in a groove, had forgotten that there was a baby in the back seat.
Both business practices and chemical operations/technologies are subject to the exact same issue of not seeing the forest because of the familiar trees. I remember our R/D staff, when moving into a new R/D facility, took great pains initially to keep the labs as pristine as the first day. However, as the first month passed, and chemical reactions and initial wear and tear took their toll, the R/D staff lost their “awe” so to speak, and the site became “just another facility”.
A plant that has been operating without incident for years tends to be self-reenforcing in terms of acceptance “of the way thing are”. The plant losses its edge, begins to tetter into decrepitude or inefficiency, while the staff sees the symptoms without understanding the root causes: raw material changes, degeneration of control loops and equipment, acceptance of “temporary” process compromises from the early days that were baked into permanence.
It can be challenging to implement new business practices and technologies while maintaining a steady state in operations – there is always some resistance to “new things”. Also – if you see the same thing day after day, you come to accept the circumstances as “normal”… “it’s just the way things are…” During one my early employment experiences, we had within our R/D Department an experienced researcher who had been responsible for the same process for over 10 years. After this period of time, he became a detriment to progress. Any suggestion about process changes would be met with – I tried that 5 years ago and it didn’t work. It was only after the researcher retired and responsibility given to a new researcher did progress begin again in optimizing the process.
Considering the above factors, it becomes clear that within the CPI, business transformation needs to take two parallel paths:
1 – Transformation of on-going business practices. Again, personnel have grown accustomed to various workflows and conventions which are perceived as normal, even if there is some understanding that these are getting in the way of profitability. In one company that I took over as R/D head, R/D was used as an extension of the Marketing Department – researchers would be sent on customer calls, and customers would call directly into R/D for information. In another company, each Salesperson appeared to have a “pet” R/D researcher that the salesperson would ask to develop new products for his customers. In both cases, R/D was fragmented and ineffective. The cure was straightforward – cut the direct link between R/D and Sales/Marketing and develop procedures to govern the interfunctional relationships.
2 – Technical transformation: every new plant has its day in the sun, when it is shiny and new, has attention lavished on it, and works like a Swiss watch. These days do not last long. Even the well-designed facility has compromises and ambiguities in its designs…. The cost of building a “perfect” operation would be infinite, so trade-offs have to occur. As time goes on, new products are sometimes shoehorned into the plant, equipment begins to wear, technologies become obsolete, maintenance is deferred, and the unit becomes a shadow of its former self.
At some point, these deficiencies become normalized and become accepted as “a new normal”; profitability declines, safety issues increase, and worker morale plunges as “finger in the dyke” management takes hold.
In this case, if the business is to maintain its viability, a fresh set of eyes (internal or external) needs to come into the plant for a systematic deficiency analysis, that parallels the analysis of business operations.
In many cases business “transformation” issues are not clear cut. The principal question that must be answered is: are we seeing the actual problem, or are we seeing the symptom of an underlying problem? The old joke of “The beatings will continue until morale improves” is sometimes the reality, not a joke; also – “blame the victim”.
As it obvious from the above discussions, before CPI companies can plan transformational projects, both for business process and technical upgrades, they must have a clear view and common understanding of just what the problems actually are. Processes in the chemical industry are complex, and any change can have unintended ripple effects on the entire operation. It is essential to have a clear understanding of the goals of these transformations and how they will affect all stakeholders, before making any changes.
Legacy Systems and Technologies – threat or menace?
No current CPI operation exists in a vacuum. Chemical companies are under pressure to keep up with the latest advancements in Business operations and chemical processing. This often requires moving from legacy platforms and technologies to more robust, high-tech tools, software, and operational methods. The transition can be difficult and expensive, but it is essential to stay competitive. Businesses need to adopt newer technologies such as automation, data analytics, and machine learning, plus the latest processing techniques. These technological overhauls require moving from legacy platforms to robust, high-tech tools, software, and technologies.
In addition, a complete audit of the plant’s technical operations is essential, and in many cases must move in tandem with business process operations – where are the bottlenecks, what is getting the way of efficient operations, does the operating staff know what to do and when.
As an example, chemical reactions and chemical formulations depend on the exact amounts of reactants/raw materials being introduced in the reactors; subsequent separation operations depend on exact conditions being applied. Sloppy procedures, inexact weights, and poorly understood SOP’s will inevitably lead to bad products, process upsets, or safety emergencies. Both for safety reasons and the delivery of in-spec products, SOP’s need to be followed exactly. But – this implies that operating personnel have access to the latest, most up to date SOP’s and process safety procedures and information. In addition, there must be an inventory system in place so that the right materials are delivered to right place at the right time. Business process transformation is an important part of this process.
Thus, appropriate solutions need to be developed consistent with business needs. Sometimes, businesses need to invest in automating their processes and systems. Sometimes this is overkill. It is essential to develop the appropriate response.
Typical strategies to be used in CPI optimization are:
-
Data analytics, both in business processes and chemical operations can help commercial concerns make better decisions by providing insights into their operations. Machine learning can automate tasks that are currently being done manually. This is crucial for businesses that want to remain competitive.
-
Inventory tracking and across-shift operations are also essential. Antiquated technology and chemical processing operating systems often rely on built in-house spreadsheets and software, along with verbally transmitted instructions to manage their inventories and operations.
These inventory and communication inefficiencies are due to manual intervention, working in silos, and not keeping a real-time track of inventory and operational procedures. However, in solving both inventory and communications issues, the reform of chemical inventory management and communication processes to an automated platform can cause chaos and mishandling . This is due to poor inventory/process data derived from legacy systems along with personnel’s reluctance to engage and change.
Aspects to consider:
Software Controls – Communications, Process Technology, Business Operations When choosing a software solution, don’t simply pick commonly used industry technology or take the advice of someone who you believe knows this technology. The choice of a technology must be carefully considered and must solve multiple business and technical issues
Software Configuration Management (SCM) is the process of tracking and controlling changes in software configurations both in business and technical applications. The goal of SCM is to ensure that the right versions of the right software components are delivered to the right locations at the right time. These must integrate correctly. SCM practices include configuration control, configuration identification, configuration status accounting, and reporting. Configuration control is the process of approving or rejected change requests against a baseline.
Configuration identification involves creating and maintaining a database or a technology stack map of all software assets and their associated configuration items.
Configuration status accounting involves recording all information related to the status of software assets.
Reporting provides visibility into the progress of SCM activities and the compliance of software assets with organizational policies.
The Unappreciated Factor: A Human Capital Shortage
The chemical industry is vital to many different processes and products that are used on a daily basis. From the food we eat, to the clothes we wear, to the cleaning products we use, chemicals play a role in nearly every aspect of our lives. As a result, chemical companies are always searching for talented and hard-working individuals to join their ranks. However, the industry is currently facing a shortage of skilled personnel, which is hampering its ability to digitize and streamline its operations.
This shortage is due in part to the unique nature of the skills required to participate in the chemical industry. Unlike other industries where technology has replaced many traditional tasks, the chemical process industries still require a human touch. As a result, there is a need for individuals who are both technologically adept and well-versed in the fields of science, plus have the ability to successfully maintain human interactions. While this may seem like a tall order, it’s essential for the chemical industry to find these specialist workers if it wants to remain competitive in the global marketplace.
Antiquated Processes
Antiquated processes are the bane of chemical companies across the board. From resource management to billing cycles, pricing strategies, report generation, and technical improvements and communications, every process is in dire need of an update. These changes can be daunting, time-consuming, and expensive, creating a massive challenge for chemical companies in their path towards streamlined operations. However, the benefits of a streamlined operation are clear.The importance of a technical assessment
Just as an army travels on its stomach (per Napoleon), a chemical plant ultimately travels on its technology. An important part of an optimization strategy is a detailed technical assessment of how a chemical facility functions:
1 – What processes take the longest time to complete and why?
2 – Is there an understanding of underlying chemical and physical processes within the plant (chemical kinetics, mass transfer, and separation issues)?
3 – What are the aspects of mixing in plant operations?
4 – Are there up to date P&ID diagrams to permit rapid troubleshooting?
5 – How is operator training (process and safety) carried out and documented?
6 – Is there a culture of safety directed from the top down?
7 – Is there a Quality System in place that is respected (ISO-9001 as an example)
8 – Is there an underlying foundation of SPC within the plant QA function?
9 – Does the plant QC/QA have the necessary respect to act as an impartial monitor?
In Conclusion
By updating their processes, chemical companies can save time and money while improving the quality of their products. In today’s competitive marketplace, that is a vital advantage. Process mapping can be a helpful tool in identifying where process updates are needed. Business process mapping provides a visual representation of current business operations, which can then be used to identify inefficiencies and bottlenecks. Technical mapping can indicate process steps that need improvement to meet overall efficiency goals.
Once problem areas have been identified, root cause analysis can be used to determine the best course of action for updating these processes. Implementing process improvements can be a major undertaking, but the benefits are well worth the investment. Streamlined operations can lead to increased efficiency and productivity, lower costs, and improved product quality – giving chemical companies a significant competitive edge.
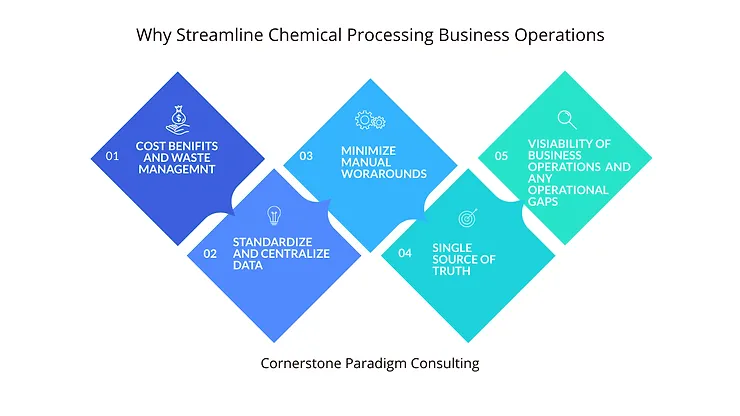
Key Takeaways
As the world progresses, so too does the way businesses operate. In order to keep up with these changing times while maintaining a successful company, it is essential for those in the chemical industry to stay up to date with digital business practices and technical advancements. This means implementing comprehensive ERP and SCM tools (Software Configuration Management) in order to streamline efficiency from the bottom all the way to the top – and even afterwards. It means taking a critical look at current technology implementation and making use of modern methods. It also means a rigorous look at the technical foundation of the plant as to its robustness and ability to reflect state of the art advancements.